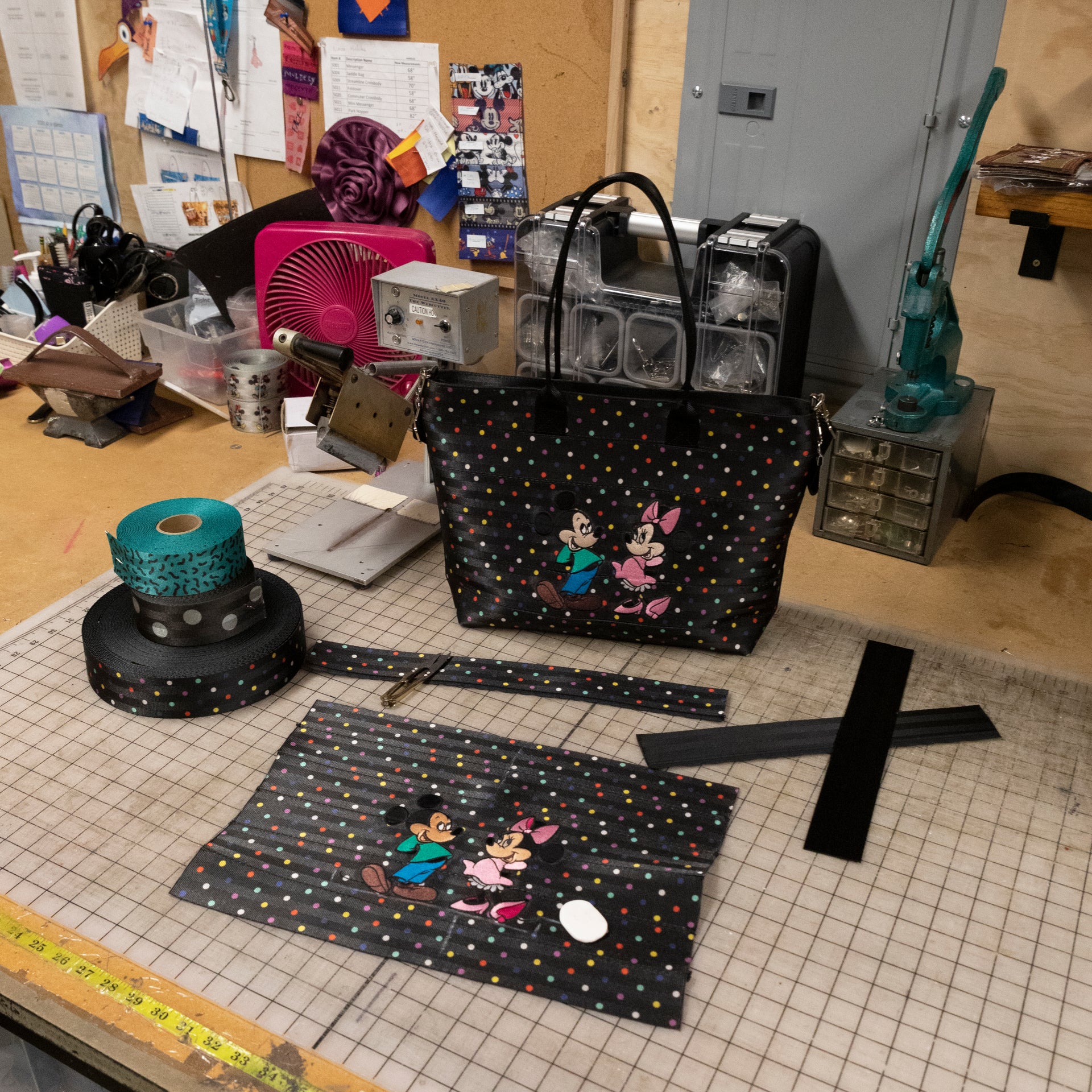
Made for Me: Sampling
Welcome to Made for Me Monday! Last week we left off with the completed digital designs and now it’s time for the sampling process. Sampling can take anywhere from a few weeks to months depending on the complexity of what’s being produced. So how do we go from digital mockups to physical seatbelt bags?
Before the designs are sent out for sampling and production, our team has to visualize how they will work in a real, 3D environment. This is very important as some designs or elements may look correct on the computer but may not translate the same way in real life. The first step is to simply print the designs out on paper. Each design is printed out on large pieces of paper and pinned to a bag. Seeing the design in a 3D space allows us to check the scale of the pattern and get a feel for the overall look of the bag. After we nailed down the size of the patterns, our team’s next hurdle is to check the scale of the characters. To do this we printed paper versions for each era of Mickey and Minnie in various sizes. These are placed onto the bag to see how the different sizes compare before we move on to testing the embroidery.
The next hurdle for our team in regards to the Made for Me project was the embroidery. This year our team purchased a new embroidery machine and were excited for the challenge of embroidering Mickey and Minnie Mouse onto our seatbelt. We love seatbelt because of its strength and durability but that means it isn’t always easy to work with! Our team is always up for a challenge and definitely put the new machine to the test! The first step in the embroidery process is selecting thread colors to best match each character’s design. After the thread colors were selected we did test runs of the embroidery to see how they would look on the seatbelt. Each piece of embroidery takes between 45 minutes to 1 hour and 15 minutes to complete!
For the printed belts, after the artwork size is approved by Dana and Melanie, the designs are sent out to be turned into seatbelt. Since we had previously used the Sprinkles and larger polka dot prints, these two were a bit easier and required less sampling. The 1980s was the only design we hadn’t sampled in a seatbelt print before and required a few rounds of sampling. When reviewing the first sample we realized the design was too large and fell too close to the edge. We lined it up on a sample bag and felt that the black lines were crashing into each other and needed more space to breathe. After reviewing the sample seatbelt, our team sends out any notes or updates and waits for a new sample. Once any new samples come back they are reviewed by our team and ultimately approved for production by both Dana and Melanie.
Once the seatbelt and embroidery were approved, they were given to our sample maker Martin to be sewn into sample bags. Martin has been working at Harveys for 17 years now and is an absolute wizard on the sewing machine! He works closely with Dana and Melanie to make our visions a reality! Once the designs are finalized and sample material arrives, he creates sample bags for each item in a new collection. With Made for Me it helped us see how the embroidery worked with the prints and how each of those was tied together with the final accents like the handle colors, zippers, and hardware. When these sample bags are completed, Martin gives them to the team for review. Depending on the collection, he may have to create many different rounds of sample bags to make sure everything is perfect for production.
Oftentimes people ask us what happens to these sample bags after a collection is released. Sometimes Melanie will keep these bags for her personal collection but sometimes they are given to our team for special giveaways or even charity raffles for organizations that we love.
Now that the samples have been approved it’s time to move on to materials! Next week we’ll be knee deep in seatbelt and lining as we prepare to begin production on the bags! Stay tuned to see how we prep the materials and all the steps needed to get production started.